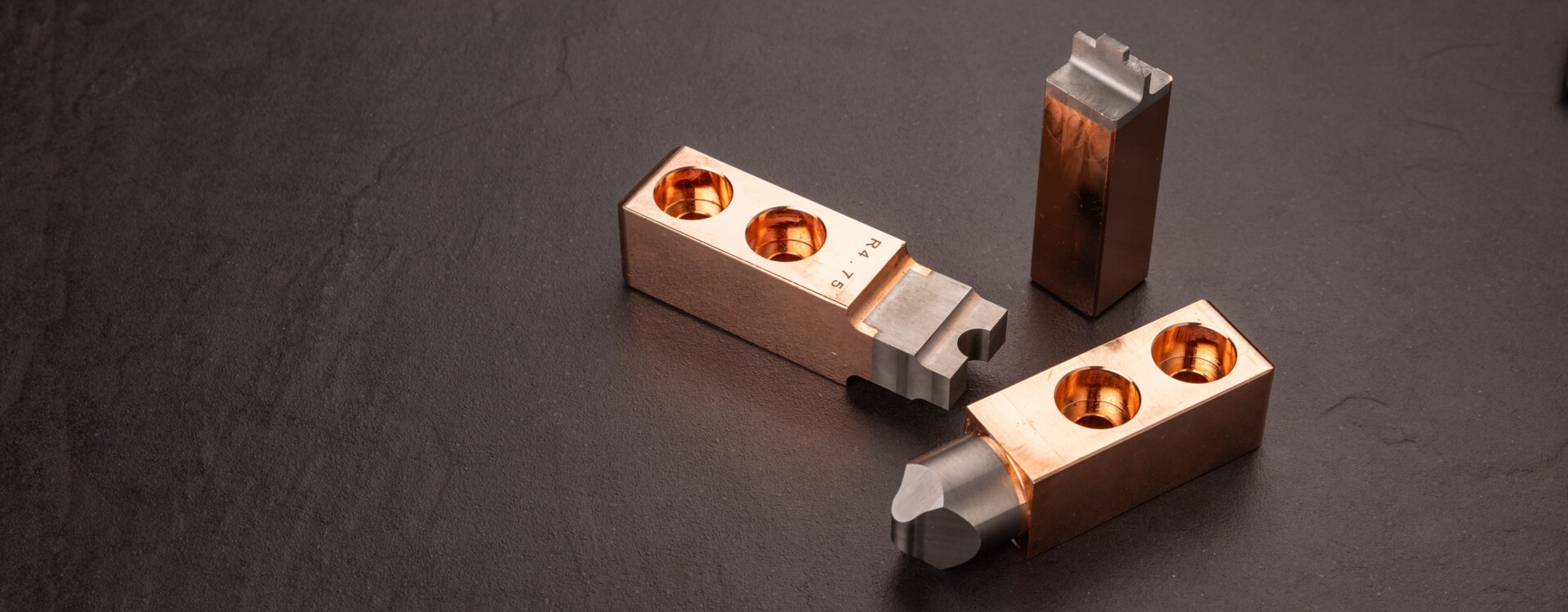
Electrodes for resistance welding
Buy high quality electrodes from Litty
High-quality electrodes are crucially important for producing reliable connections. The experts rely on materials such as tungsten, molybdenum, copper, tantalum, TZM, tungsten heavy metal and their alloys in the production of resistance welding electrodes. The electrodes are particularly suitable for welding materials with a high degree of conductivity such as copper.
The advantages:
- High temperature resistance & density
- High degree of thermosetting
- Outstanding electrical and thermal conductivity
- Excellent machining capability
- Low welding tendency
- Long service life & efficiency
- Constant resistance during the welding process
- Good flammability and long service life
- Radiation free and environmentally friendly
Resistance welding electrodes from Litty provide precise welding results.
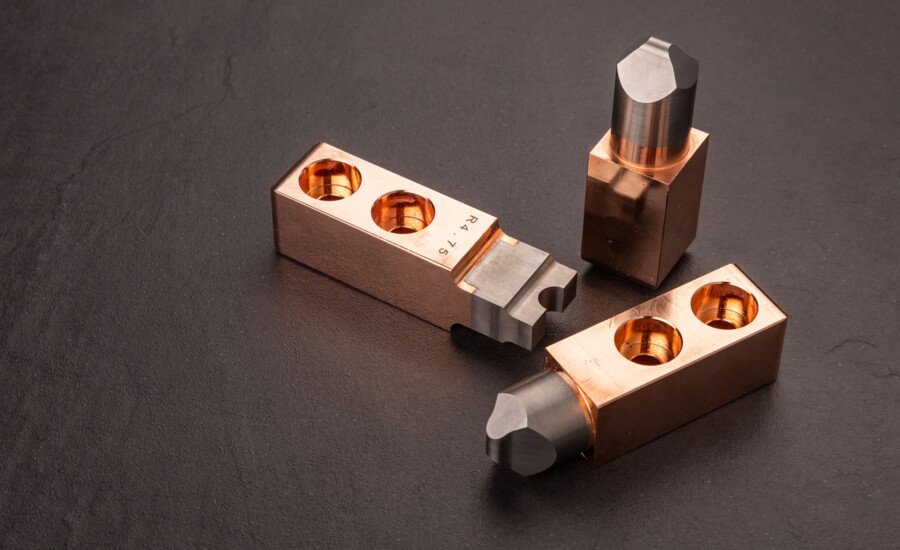
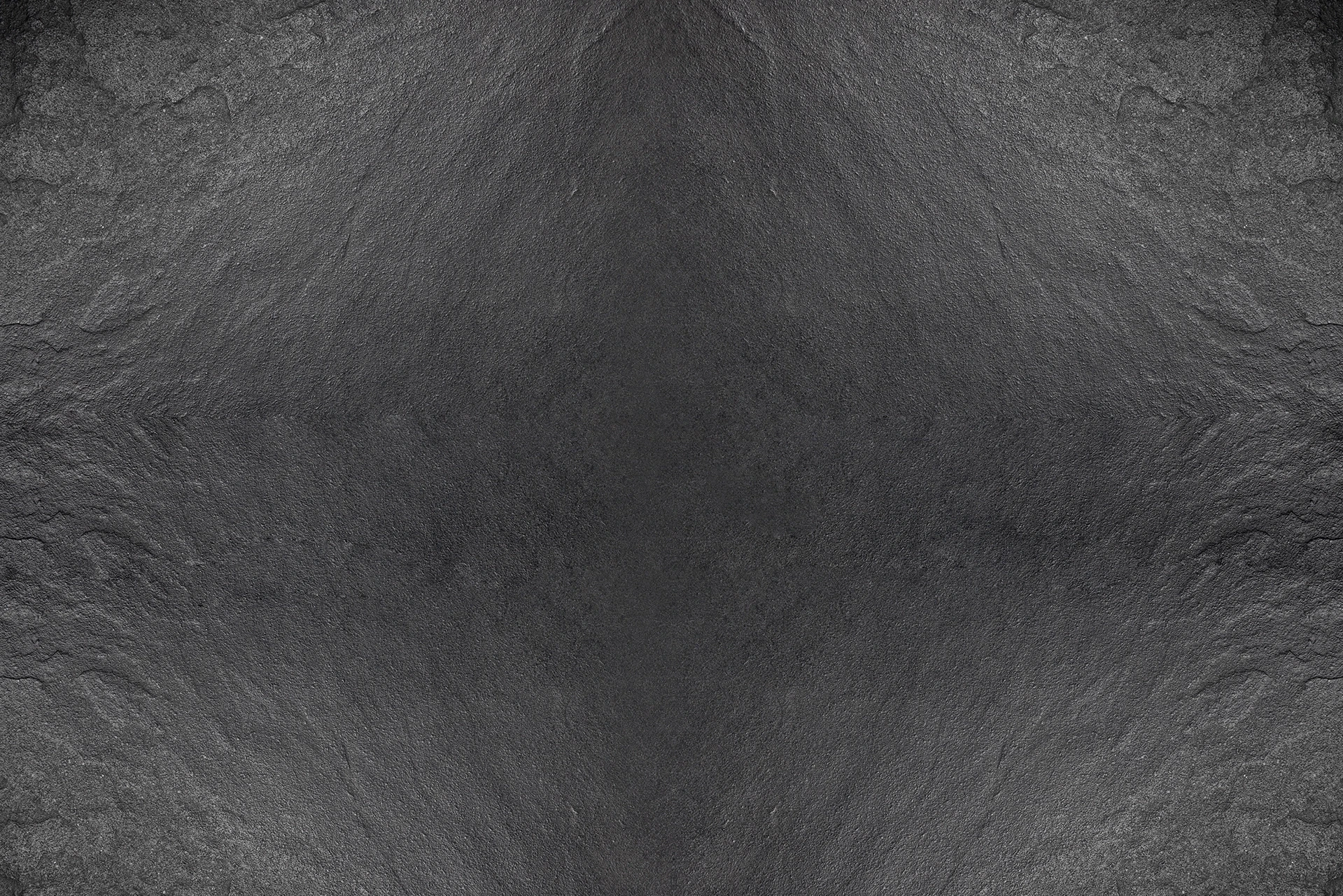
Buying electrodes for resistance welding: quick and easy
We are your partner for high-performance electrodes for resistance welding, and would be pleased to fulfil your requirements. Put your trust in the well-tried Litty service. You will receive resistance welding electrodes from us made from tungsten, molybdenum and their alloys.
We would be pleased to provide you with top quality resistance welding electrodes, and can also manufacture in accordance with your individual requirements. We will ensure that you receive your products in a reliable, quick and uncomplicated manner.
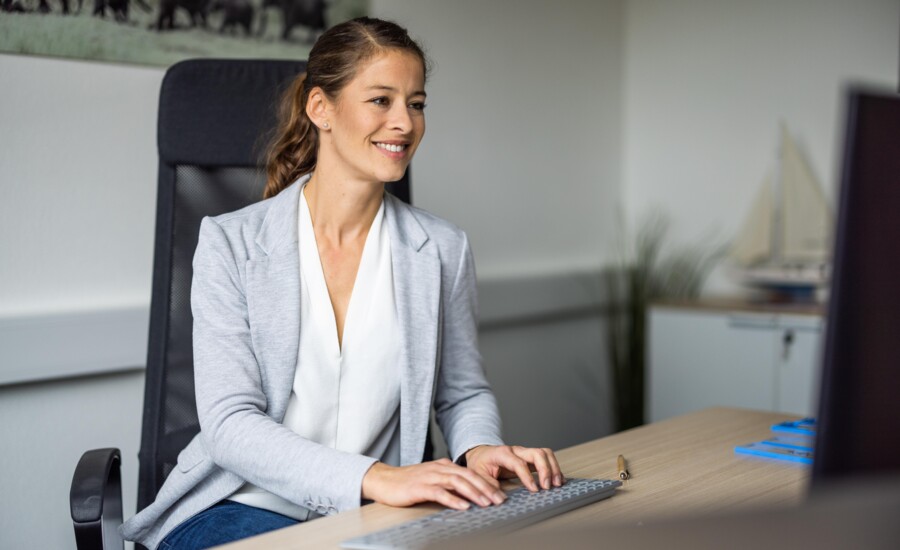
Resistance welding electrodes
An overview
Solid material electrodes
These are manufactured from:
- W, WL10
- Mo, TZM
- WCu70/30, WCu75/25, WCu80/20, WCu90/10
- Tungsten heavy metal alloy
- We would be pleased to manufacture in accordance with your individual requirements at Litty
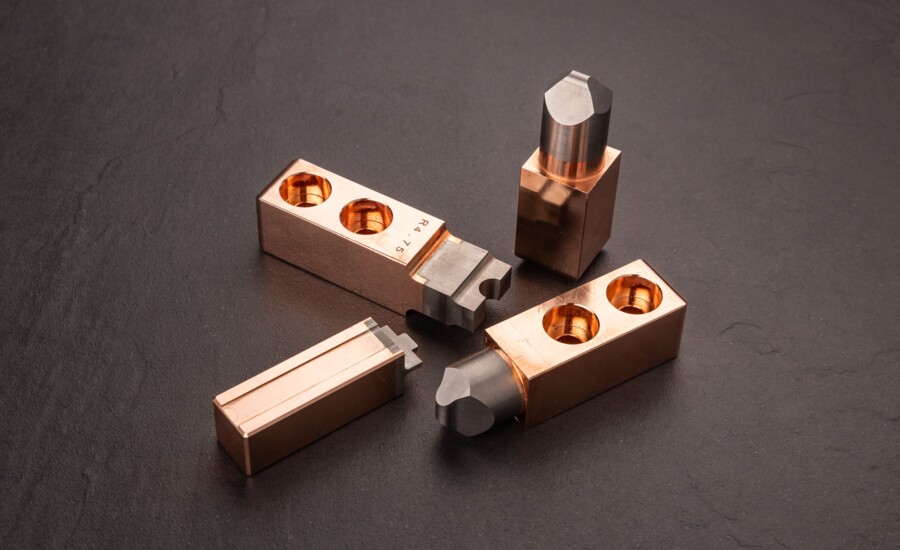
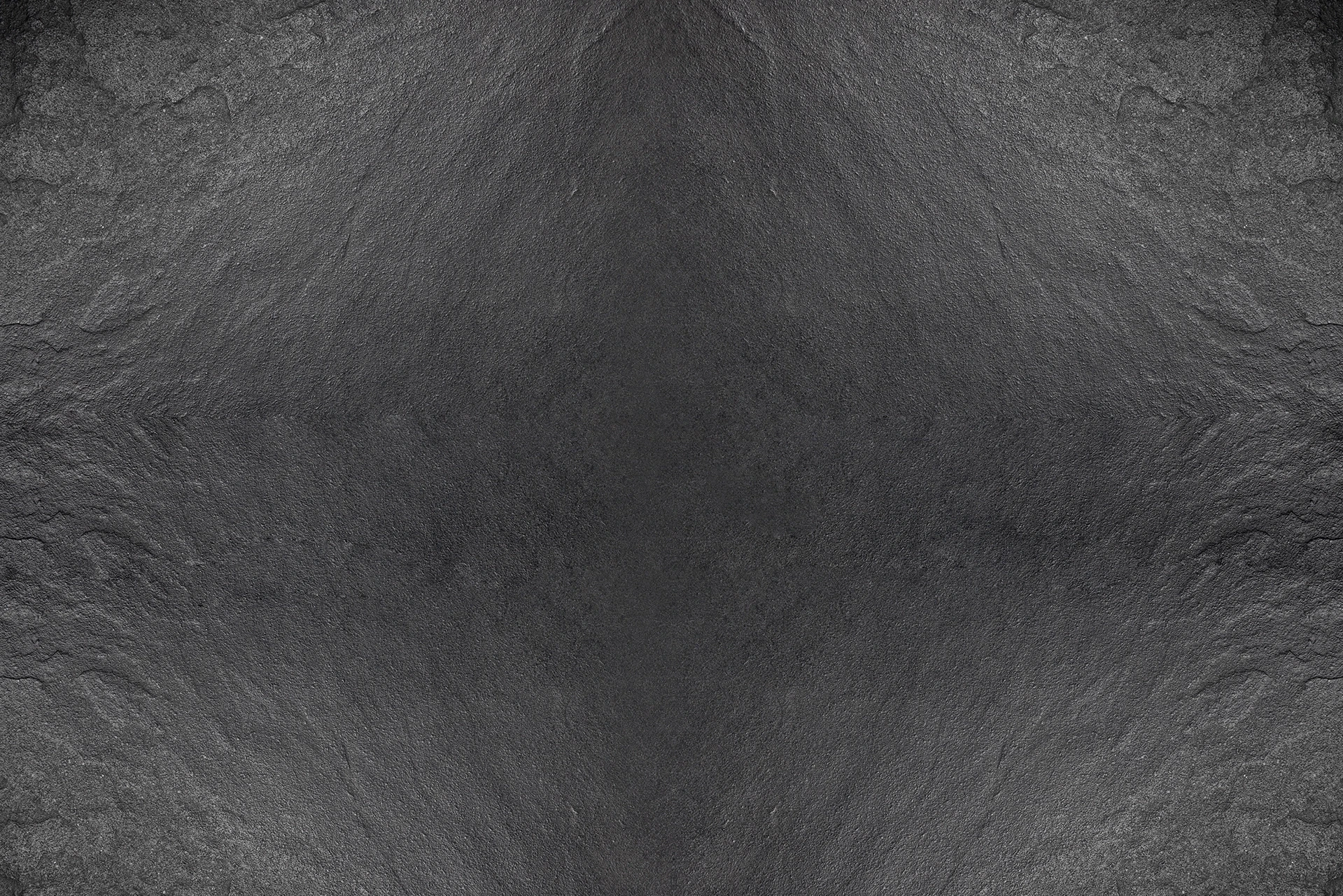
Back-cast electrodes
These electrodes are also known as insert electrodes, and are manufactured from:
- CuCrZr shaft with W, WL10, Mo or TZM insert
- Cu shaft with W, WL10, Mo or TZM insert
- We would be pleased to manufacture electrodes in accordance with your individual requirements at Litty
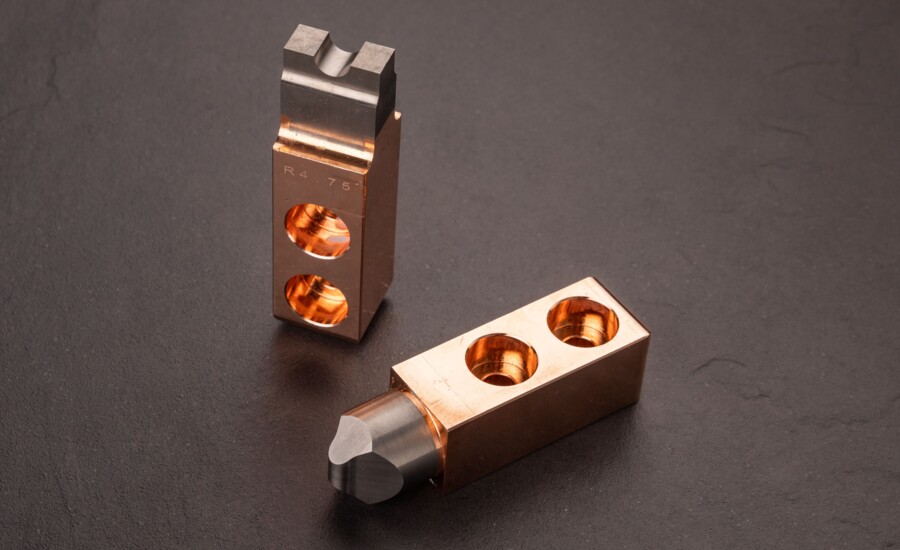
The areas of application
Resistance electrodes are used in:
- Spot welding
- Roller seam welding
- Projection welding
- Resistance butt welding
- Resistance stud welding
- Capacitor pulsed welding
- Flash-butt welding
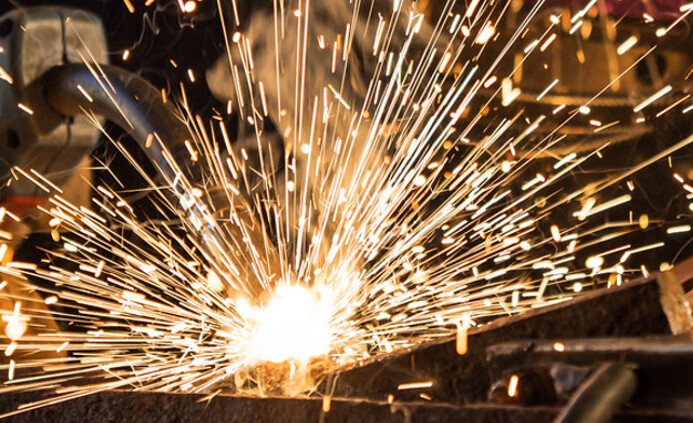
Good to know
In resistance welding, it is extremely important to use electrode materials with outstanding hardness and strength at the application temperature. These properties must be retained, even after prolonged exposure to heat. The materials must also have a high softening temperature and tempering resistance. Did you know that tremendous forces of up to 450 megapascals (MPa) can occur between the electrode and the workpieces to be joined when thick sheets or similar workpieces are being welded? It is important for the electrodes to be able to withstand these stresses. This is the only way to achieve reliable welding results.
Would you also be interested in other electrodes? Would you like to discover more about plasma spraying , Lymox electrodes or our special grinding service? You will find an overview of welding electrodes here. Or would you like to send your inquiry to us directly?
FAQ
Resistance welding is a joining process in which workpieces are attached to each using pressure and electrical resistance. Due to the high current flow and the resulting heat, the material melts and forms a solid weld seam after cooling It is used in various industries, and has advantages such as efficiency, working speed and the reproducibility of the weld seams.
Resistance welding is used in various industries, particularly ones which make high demands with regard to efficiency, precision and production speed. Industries in which resistance welding is frequently used:
- Automotive industry: Welding of body parts; particularly for welding sheet metal components and manufacturing chassis components.
- Electronics industry: for the manufacture of electronic components, particularly for the manufacture of circuit boards or connecting cables and wires.
- Aerospace: for aircraft structures and engine components.
- Construction industry: Metal structures and steel structures, welding of metal parts for construction projects.
- Household appliance industry: Washing machines, dryers and refrigerators.
- Power generation: Manufacture of components for power plants.
On the whole, back-cast electrodes have a longer service life, better heat dissipation, reduced oxidation and optimal current distribution, which results in improved weld quality and efficiency.