Refractory metals in the aerospace industry
Withstanding high temperatures with confidence
It’s the heat resistance and melting points that make high performance metals so indispensable in aerospace. Tungsten, tungsten-copper, tungsten-heavy metal, molybdenum, tantalum, niobium or alloys with these metals make it possible to produce components that are suitable for use in rockets, space stations or jets. Molybdenum is mainly used as an alloying additive in steel, tantalum as an additive for aluminium, and tungsten is used as an alloying additive in steel and aluminium. The result brings hardness, strength and high thermal conductivity. Would you like to know more about the properties and melting points of the various refractory metals?
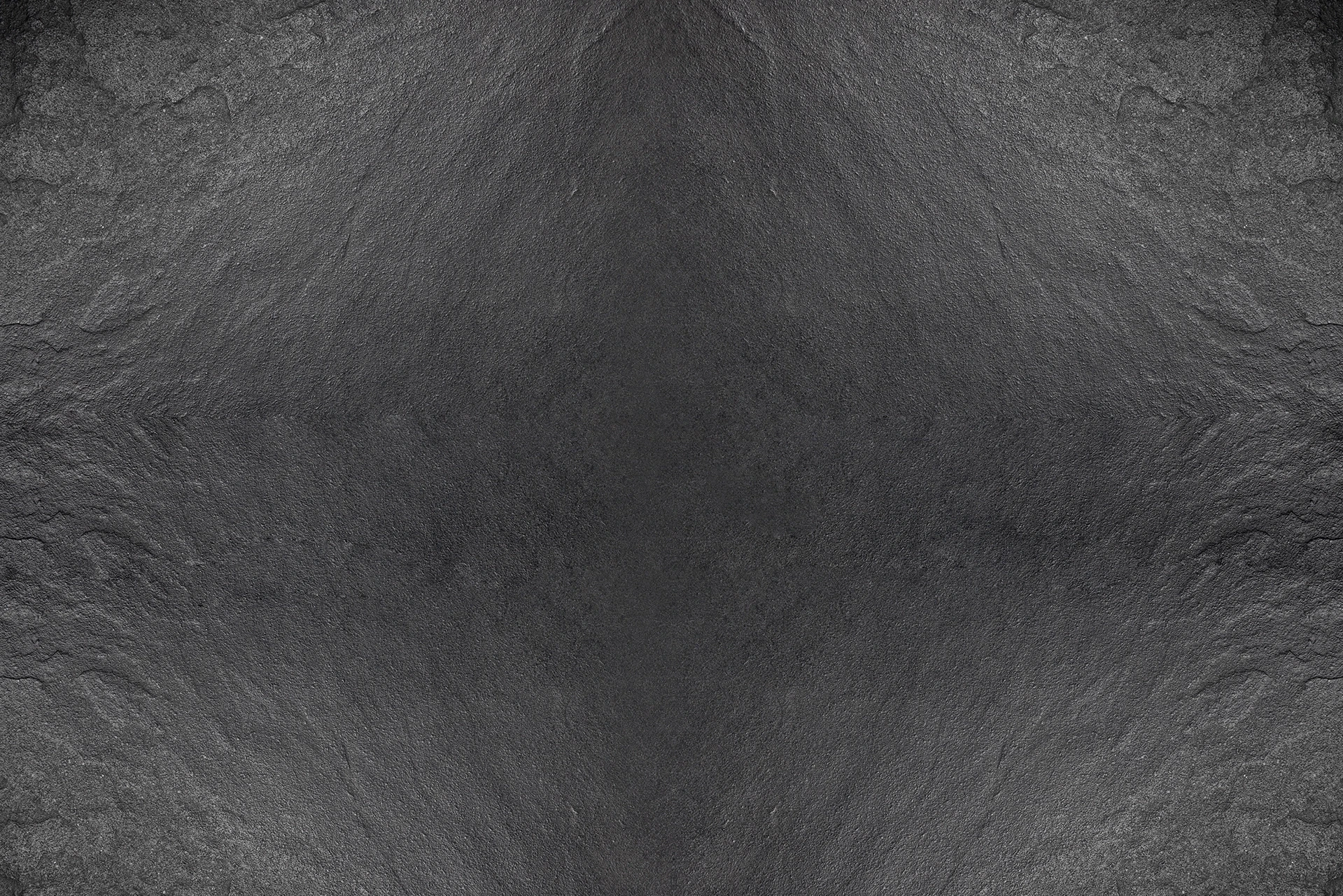
Use of refractory metals in the aerospace industry
Refractory metals are used in the manufacture of aircraft and rockets because there are high temperature differences in the troposphere, stratosphere and outer space. Examples of application:
- Aircraft & rocket parts
- Nozzles
- Combustion chambers
- Heat shields
- Engine components
- Tools
- Gearboxes
- Landing gear
- Turbines
- Generators
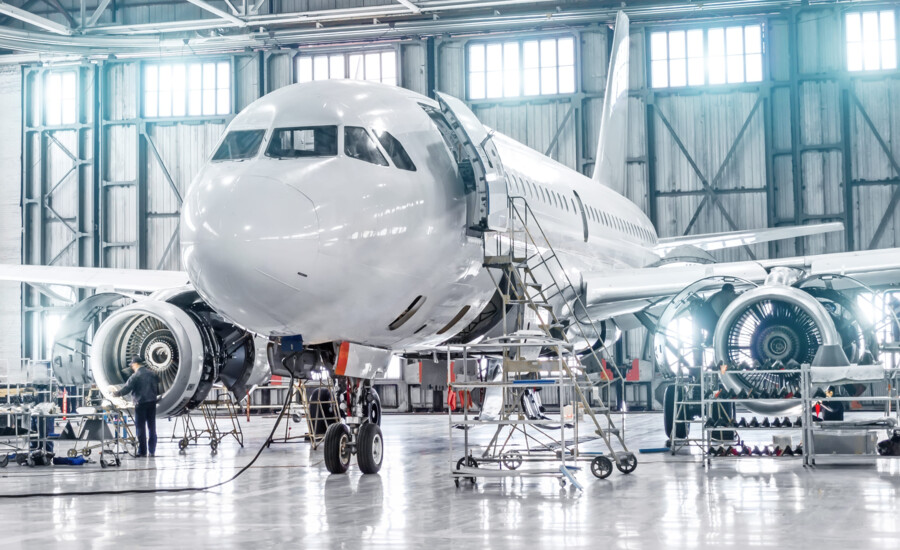
Good to know
Refractory metals played an important role in the manufacture of components for NASA’s Space Shuttle, among other things. The manned space shuttle was in service from 1981 to 2011. Here, too, refractory metals were indispensable companions to success. Tungsten and molybdenum, for example, increased the hardness and strength of components. In electronic components, too, it was the refractory metals that improved heat resistance and reliability under the extreme conditions in space.